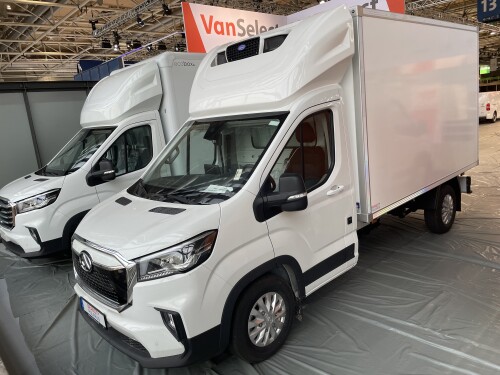
The prototype of the electrified refrigerated vehicle attracted a good deal of interest during IAA.
It all began with VanSelect and IAA: In this interview, BRANDT*POLARUS Managing Director Dr. Christoph L. Heger-Bismark explains how the individual refrigerated vehicle was developed, its components as well as its advantages and suitability for everyday use. After all, the field of temperature-controlled transport brings with it a number of challenges. Customers know this best - and they are very interested in the vehicle.
Chassis: Maxus eDeliver 9
Range: 160 km
Cooling capacity: 2,300 W
Payload: 750 kg
Total weight: 3,500 kg
Vehicle energy consumption: combined (WLTP) 32.4 kWh/100 km.
“There are three key issues with an electrified refrigerated vehicle: constant cooling, range and vehicle weight or payload,” says Dr. Christoph L. Heger-Bismark, Managing Director at the body manufacturer BRANDT*POLARUS. He goes on to explain: In a classic diesel vehicle, the cooling system is supplied with energy from the combustion engine via a belt drive.
This does not work for the electric transporter, because on the one hand it is technically difficult to supply the cooling system via the traction battery, and on the other hand this leads to a loss of range. In addition, it should be possible to operate the cooling machine even when the electric vehicle is switched off, e.g. during delivery. But this is not possible if the energy is supplied via the traction battery. “The most sensible solution is therefore an auxiliary battery.”
The prototype of the electrified refrigerated vehicle attracted a good deal of interest during IAA.
The problem is solved by means of a powerful auxiliary battery, which supplies the cooling system with energy independently of the traction battery. However, the third sticking point must be taken into account: “Electric transporters are fundamentally heavier than diesel vehicles due to their drive. It is essential therefore to ensure that the additional battery is not too large on the one hand and not too heavy on the other. The payload is a decisive criterion,” says Heger-Bismark. If it is too low, the vehicle is simply not suitable for everyday use by customers.
“The XBU is therefore ideal because the battery can be installed behind the passenger seat thanks to its flat design and is not too heavy.” In addition, he says, the nickel-cobalt cells are a great advantage because they are far less temperature-sensitive than the usual lithium-ion batteries with different cell chemistry.
But how did the construction of the showpiece superstructure actually come about? “We are members of the VanSelect industry network together with other companies”, reports Heger-Bismark. At IAA Transportation 2022, there needed to be a particularly innovative vehicle on the VanSelect stand. To this end, the electric refrigerated vehicle was developed together with Maxus, Carrier, X-Tronic and LEAB under the leadership of BRANDT*POLARUS.
The cooperation between all the partners has worked superbly. Together we have mastered the challenges of this kind of set-up, acquired a great deal of expertise and brought a future-proof concept onto the road.
Asked why this superstructure fits in perfectly with the times, Heger-Bismark is quick to provide an answer: “The 3.5t base is the first in the transport sector that can be effectively electrified - at least for applications with a relevant route profile, such as inner-city deliveries. For our customers, this is very important in terms of carbon footprint and sustainability.” Not least for this reason, the IAA vehicle also has a photovoltaic system on the roof.
“The warmer it is outside, the more energy is needed for cooling. That's why we use the sun as a source of energy,” explains Heger-Bismark. Inside, a 4.2 kWh XBU provides the ideal mix of abundant energy and low weight. This is the elementary component of LEAB's Energy Unit solution, which also includes battery management system charge booster and the Melfbox as a 230 V input.
“From chassis to cooling system to superstructure and additional battery - we have managed to make all components fit together ideally,” summarises Heger-Bismark. The feedback from the market is equally positive. There is great interest in the body from dealers and OEMs. “We are looking forward to building the first series of this vehicle soon.”